旋盤ができる加工種類を学べる!
いまさら聞けない「旋盤の基本」を復習ができる!
旋盤ができる加工
外周削り
外丸削り
ワークの外側を円筒状にけずること。旋削で基本的な削り方です。

外径溝入れ
円柱外周面に溝を削ること。狭い溝ではバイト刃先幅を溝幅として溝寸法を管理することが一般的です。

ローレット掛け
ワーク外周面にローレット目をつけること。ローレットとはこんな形状のことで、滑り止めとして使われることが多いです。
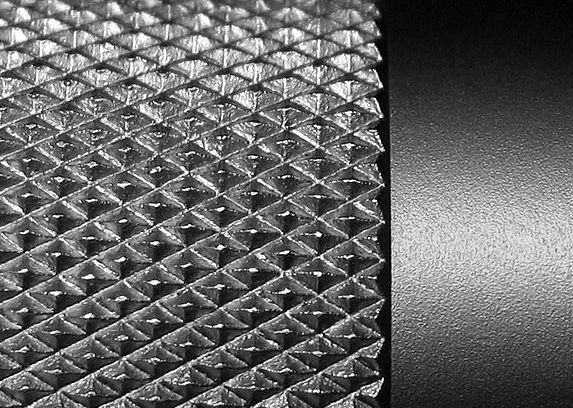
総形削り
輪郭形状をしている工具で旋削することで、所要の輪郭形状にすること。
曲面削り
下記2パターンどちらかで曲面形状に旋削すること。
①一般的な工具を使って倣い装置による倣い削りをする方法
②総形バイトを使って総形削りをする方法
突切り
幅の狭い突切りバイトを使ってワークを切断すること。
ちなみに、突っ切りバイトでは『①加工始めの端面加工 ②円柱の外周面に溝を入れ ③加工終了時にワークの切り落とし』に使うことが多いです。

テーパ削り
ワークを傾けたり、刃物台を傾けたり、刃物を斜めに動かしたりしてワークにテーパをつけること。
内周削り
内径削り(中グリ)
すでに空けられている穴を繰り広げる切削加工のこと。
大きな穴を空ける際には、現場で使っている最大径のドリルで穴あけ加工をしてから、次の工程で中ぐりバイトで所定寸法に加工します。また、ドリルでは加工精度が出ないので、精度の高い穴や、内面を滑らかにしたい場合にも、この中ぐりバイトで仕上げます。中ぐりバイトは、穴ぐりバイトやボーリングバーとも呼ばれています。

内径削り加工には3つの難しさがあります。
①加工面が見ずらいので切れ味を確認できない
②切粉が排出されにくい
③深穴の場合にバイトが倒れてしまうことでの精度不良
内径溝入れ
穴の内周に溝を入れることで、リセッシングとも呼ばれます。
リーマ仕上げ
穴の内周面の表面粗さを整える仕上げ加工のこと。
はめあいによくつかわれるH7公差といった高精度の穴加工をする場合に使われます。

面削り
端面削り
バイトでワークの端面を平面に削ること。主軸の回転速度が一定なら、切削点が中心に近づくにつれて切削速度が遅くなります。切削速度が遅くなることで加工能率が落ちることはもちろん、ビビリの原因になるので、NC旋盤なら”周速一定制御”といった機能を使って切削速度を一定にすることが多いです。

正面削り
正面旋盤を使って、大径円盤面の平面を削ること。
端面溝入れ
端面に円形の溝を切ることでトレパニングとも呼ばれます。

面取り
端面のカド・スミを斜めに削ることで、”バリ取り”とも呼ばれます。丸みをつけることを”R面取り”と呼び、斜めにまっすぐ面取りすることを”C面取り”と呼びます。
ネジ切り
バイトによるネジ切り
ねじ切りバイトで外径(おねじ)または内径(めねじ)にネジを切ります。
ネジ加工では、1回で加工するのではなく、数回に分けて徐々に切り込んで完成させます。特にネジ加工で難しいのが「切り上げ」と呼ばれるおねじの不完全ネジ部の加工です。徐々にらせん溝の深さが変わるので、高度なスキルを必要とします。
タップ、ダイスによるネジ切り
タップで内径中心部にめねじを、ダイスで外径におねじを切ります。

穴あけ
おもにドリルを使ってワークの端面の回転中心に穴を空けること。
「センタドリル」・「ドリル」・「リーマ」といった工具を使用します。旋削加工では、ワーク端面の中心部にしか穴あけ加工はできません。端面中心部から外れた部分への穴あけや・ワーク側面への穴あけ加工するには、 回転工具を搭載できるNC旋盤を使って加工します。よく”M(ミーリング)軸付きNC旋盤”と呼ばれます。

その他
センタもみ
センタドリルを使って、センタ穴を空けることで、芯立(しんたて)とも呼ばれます。

二番取り
切削工具の切れ刃の背後に逃げ面を削ること。
楕円削り
円筒外周を楕円に仕上げることで、オーバル加工とも呼ばれます。
ポリゴン加工
円筒外周を多角形に加工すること。刃物と主軸の回転比を2:1に同期させて、ワークの外径を多角形に加工します。刃物が1枚なら2面取、2枚なら4角形、3枚なら6角形の加工が可能です。

チャッキング方法
ワークをチャックで保持することをチャッキングといいます。このチャッキングでは、ワークの「固定」と同時に、旋盤回転中心とワークの中心を合わせる「位置決め(心出し)」を行う必要があります。
ワークのチャッキング方法について学びましょう!
3つ爪スクロールチャック:一般的に幅広く!
4つ爪インディペンデントチャック:角ワークや異形ワークを加工する時に!
磁力チャック:低回転、磁性ワークを加工する時に!
コレットチャック:小径ワークを加工する時に!
心押し台のセンタ:細長いワークを加工する時に! ※チャック+センタで使います
3つ爪スクロールチャック
主流のチャックです。チャック側面の穴に着脱式のハンドルを差し込んで回転させると3つの爪が中心に向かって同時に動きます。これによりワークの固定と位置決めを同時に行うことができます。
この爪には、硬爪と生爪の2種類があります。
硬爪はワークの直径が変わっても使える標準品です。焼入れされているので耐摩耗性に優れていますが、ワーク表面に傷をつけてしまいます。対策として爪とワークの間に薄いアルミ板を挟むことがあります。
一方の生爪はワークごとにあわせて作る旋用品です。高精度の加工が必要な場合に使われます。生爪での旋盤加工する手順として、まずは”生爪成形”をする必要があります。ワークをチャッキングする前に、生爪を旋盤に取り付けて、生爪をワークの外形寸法に合わせて加工します。生爪成形をしたら、旋盤とワークの位置決め(心出し)はバッチリです。
スクロールチャックには、おもに『3つ爪』と『2つ爪』があります。
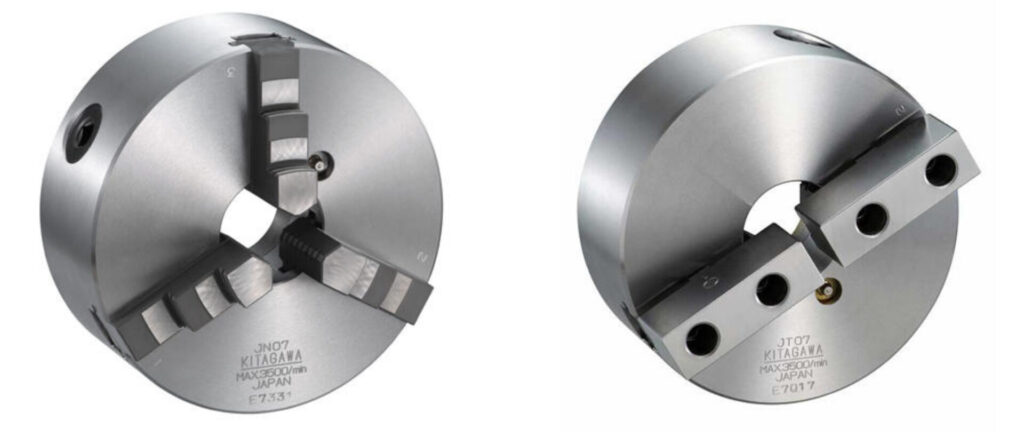
4つ爪インディペンデントチャック
4つ爪単動チャックとも呼ばれます。単動の名前の通り、4方向を個別に調整できるので、角形状や異形状のワークを保持する場合や、端面の中心以外に穴あけなどの意図から偏心させたい場合に使用します。ただし、それぞれの爪を個別に調整する必要があるので、心出し作業の手間と時間が多くかかります。

磁力チャック
爪で把握できないような異形状かつ磁性のあるワーク加工の時のみ限定的に使うことが多いです。物理的な保持ができないので、通常よりもだいぶ加工条件を落として旋削する必要があります。
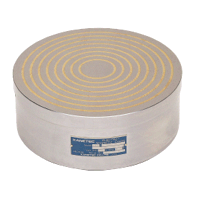
コレットチャック
直径が小さなワークでは、コレットチャックが使えます。広い面積でワークを保持できるので、傷がつきにくく、薄肉パイプ加工やアルミや銅といった軟材のワークに適しています。また 位置決め (心出し)作業が必要ないので、段取り時間も短く作業できます。
ただ、ワーク直径ごとにコレットチャックを用意する必要があります。

心押し台のセンタ
ワークが細長い場合には、ワークの右端面を支えることでワークの位置を安定させます。このワークをさえる部品を”センタ”と呼びます。ワーク材質と要求精度にもよりますが、目安として直径に対して長さが4~5倍以上の長さがあるワークにはセンタを使用します。
センタの種類には、固定センタ(デットセンタ)と回転センタの2種類があります。
固定センタは一体構造なので、ガタつきがないので回転精度が高いです。ただ、接触点の摩擦熱によって熱膨張してしまいます。
回転センタはベアリング内蔵しているので、センタとワークが一緒に回転するために、摩擦熱がおきることはありません。ただ、固定センタと比較して回転精度は劣ってしまいます。
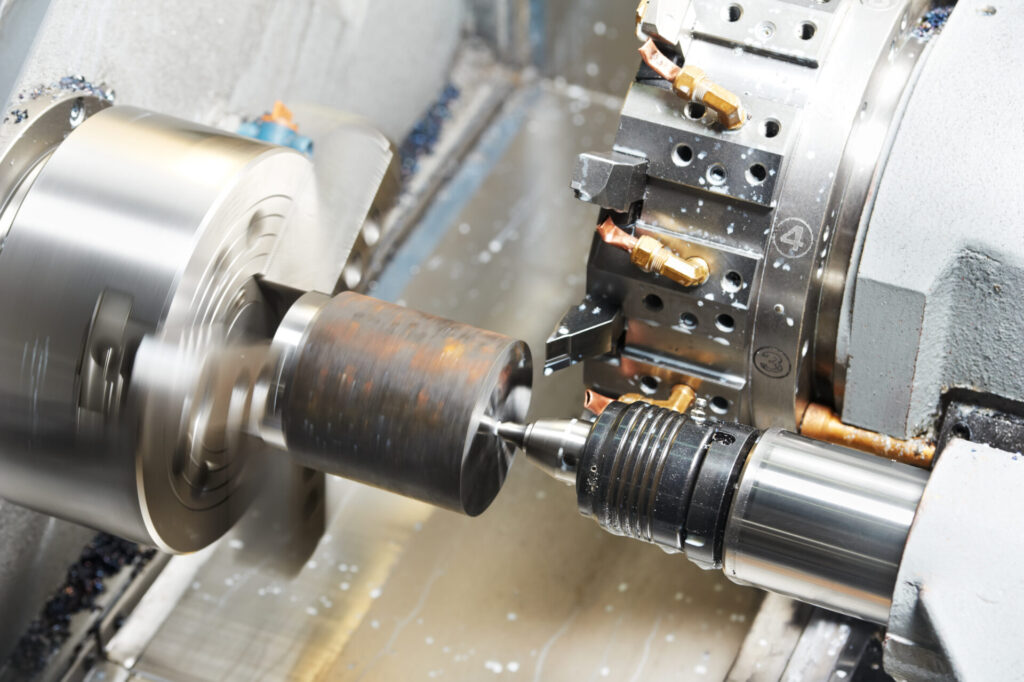

ちなみに、バブル期以前の職人さんは心押し台を「オシコップ」と呼ぶことがあります。
「オシコップ基準で〜〜」と言われても「,,,は?」って顔をしないであげましょう。笑

旋盤加工の3条件
ワークやバイトの材質、要求加工精度(荒削りなのか仕上げ削りなのかによって条件は変わりますが、どの旋盤種類にしても下記の3つの加工条件のバランスの調整が、オペレーターさんの加工スキルになってきます。
(ワークの) 回転数:加工効率とバイトの磨耗のバランス
(ワークへの) 切込み量:加工精度と加工効率のバランス
(工具の) 送り速度: 加工精度と加工効率のバランス 計算式は『送り量 × 回転数』
(ワークの) 回転数
バイトがワークを削る「切削速度」を、1分間に削り取る長さを(m/分)で表記します。同じ回転数でもワークの直径が大きくなるほど、切削速度は速くなります。そのために、最適な「切削速度」を決めてから、ワークの直径を考慮して「回転数」を計算します。
回転数は1分間に何回転するかを表したもので、単位はrpm(回転/分)です。
端面の加工は、中心部に近づくほど低速になります。加工後の端面を観察すると、中心部から外周部にいくほど光沢感があり滑らかな表面になるのは、この切削速度の違いによるものです。
加工効率を考えると、切削速度は速いほうがいいのですが、バイトの磨耗が激しくなることから、加工効率とランニングコストの経済性の2面から切削速度を決めましょう。
(ワークへの) 切込み量
1度にたくさん削るのか、ほんの少し削るのかを決めるのが2つめの加工条件です。バイトがワークを削り取る深さを「切込み量」といい、単位はmmです。
切込み量は大きいほどたくさん削れるので、切削の繰り返し回数が減って加工の効率が良いのですが、その反面で加工精度が粗くなってしまいます。荒加工では切込み量を大きく(たとえば片側3mm)して加工効率を高めて、仕上げ加工では切込み量を小さく (たとえば片側0.5mm) して加工面精度を高くします。
要求加工精度と加工効率のバランスで、切込み量を決めましょう。
(工具の) 送り速度
ワークが1回転したときにバイトが移動する距離を”送り量”といい、単位はmm/回転です。この「送り量(mm/回転)」に「ワークの回転数(rpm=回転/分)」を掛け算すると「送り速度(mm/分)」に換算することができます。
切込み量と同じく、送り速度が速いほど加工効率が高まりますが、加工表面は粗くなります。
逆に 加工条件のバランスが悪いと”びびり振動”が起きてしまいます。
びびり振動が起きると加工面がガサガサになってしまうし、異音が発生してしまうし、工具へのストレスで磨耗が急進してしまいす。びびりの要因をまとめます。
①機械によるもの:主軸や摺動面などのガタつきによる振動、加工条件のアンバランスによる加工負荷
②ワークによるもの:長軸物・薄肉形状
③刃具によるもの:バイトシャンクの剛性不足
④ワーク/刃具の取付によるもの:重量ワークや刃具の取付け不良
表面粗さの加工条件
加工した面の表面粗さは、バイト先端の半径である「ノーズ半径」とバイトの「送り量」(1回転で進む量)が影響します。旋削加工は工具の形状がそのままワークに転写されるので、ノーズ半径が大きくて送り量が小さいほど滑らかな面に加工することができます。
イメージ図を作りました。
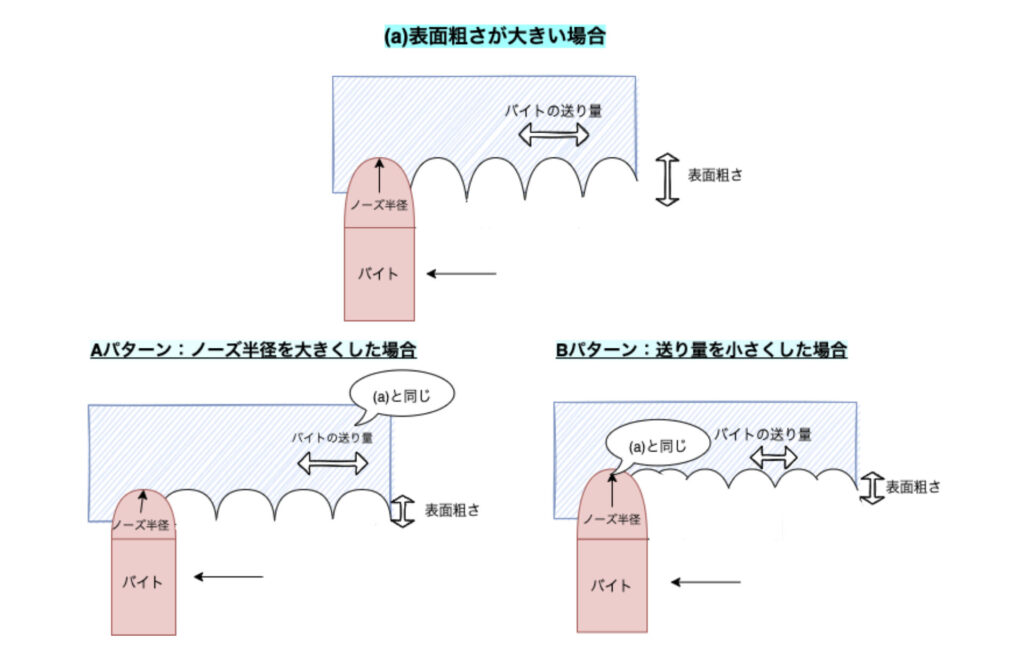

加工の組み合わせと加工方法の工夫があれば、旋盤1台で本当に幅広い加工ができます。
次回は旋盤の種類と選定基準について取り上げます。
ではまた!!
コメント